lightweight
automotive exterior decoration
automotive interior decoration
automobile electronics
echom-乐游app官方下载
the development of the front-end module materials has gone through different periods, from the beginning of the use of steel manufacturing to form the headlight bracket, gor, to the current mainstream into a full-plastic front-end module (fem). for example,from injection molding with pa,pp,lft,pp-lgf,gmt and other materials to the latest front end module structure made of metal-plastic composite, the development of front end module also reflects the design progress of front end module in material,process and structure.it brings more comprehensive consideration of the production cost, production efficiency, manufacturing process, performance requirements, lightweight and other issues brought by the automobile front-end module.the front-end module technology is becoming more and more mature, and it is more and more widely applied to different class of cars.
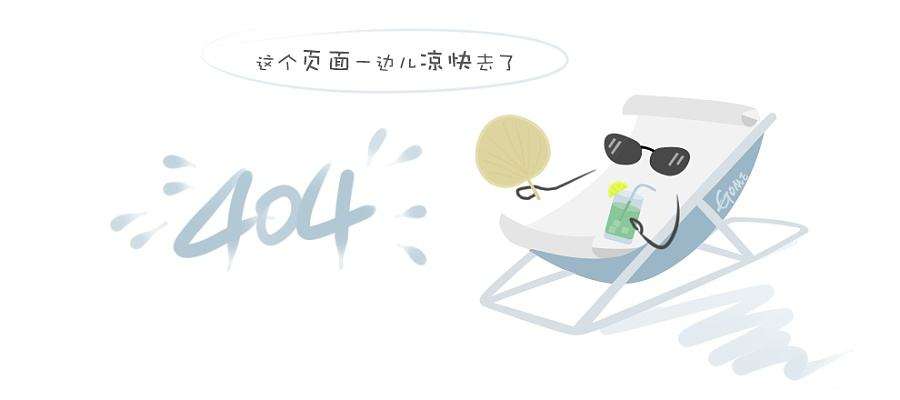
the plastic back door is about 30% lighter than the sheet metal structure.as the internal and external parts are integrated, the number of parts is reduced and modularized
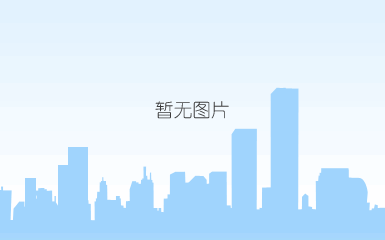
in the automobile injection mold, the automobile bumper product usually adopts the advanced internal parting surface technology in the mold design.the advantage is that the parting clip line is hidden on the non-appearing surface of the bumper, and the appearance of the clip line is not seen after assembly on the car, which will not affect the appearance of the product.
high-gloss seamless injection molding technology is applied on the bumper grille, which can reproduce any shape of the mold surface, so that the surface of the product has no melt marks, no flow marks, no flow lines, no shrinkage marks.surface highlight achieves mirror effect. improve the strength and surface hardness of injection molded parts;no need for subsequent spraying processes with serious environmental pollution, reducing technics process flow and saving energy and materials
hot stamping technology applied on bumper grille.the hot stamping and the traditional electroplating products have similar appearance effects, and the electroplating process is replaced within a certain range on the outer trim parts to reduce pollution and reduce the use of the electroplating process.
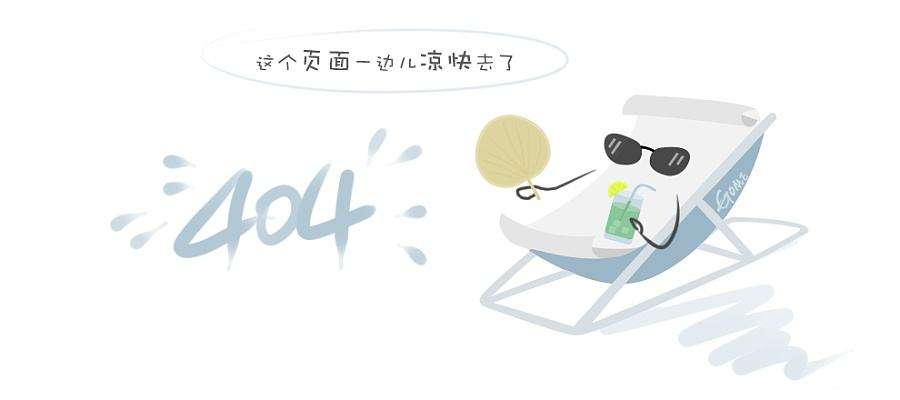
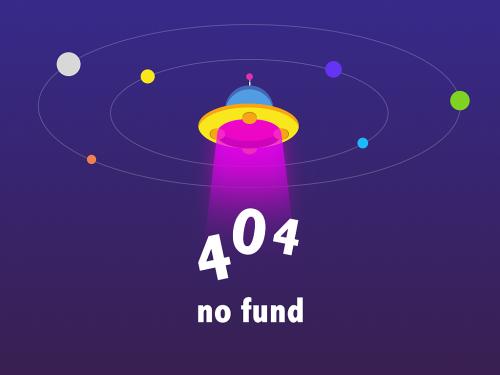
high gloss spray free
hot stamping
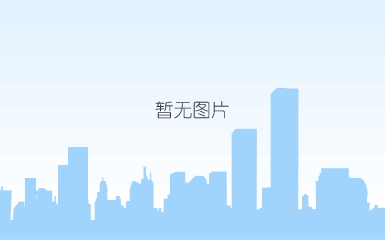
plastic fenders are about 30% lighter than sheet metal structures.self-resilience ability for minor collisions
-
the dashboard applies laser weakening technology (pab), vibration friction welding technology, female molding true seam line forming,male molding, iml (in-mold insert), high-gloss spray-free technology, double-color injection molding
-
door guard applies female mold true seam line forming, male molding, iml (in-mold insert), high-gloss spray-free technology, two-color injection molding
-
the female molded skin itself has no pattern, and the pattern is on the female model cavity. it has the advantages of good replication effect and high production efficiency.but,at the same time, it has high requirements on equipment and needs high investment in mold cost
-
iml and ins process is a commonly used plastic surface treatment process, which is widely used in dashboard, central control, door trims and other parts.the iml diaphragm substrate is made of pc material and the film thickness is thin; while the ins is abs pmma, the film thickness is thick.the former has excellent temperature resistance, while the latter has better tensile properties with the addition of abs.compared with iml,ins has higher product tension and is suitable for the interior surface of complex curved surfaces, which can reduce the pattern deformation to the greatest extent. iml is more used for low-stretch products, such as dashboard panels.
the vacuum absorption of the male mold has the advantages of small investment in mold, long service life and high production efficiency.since the skin pattern is pre-made, the pattern will become lighter during the stretching of the skin and there will be restrictions on the rounding of the part.
laser weakening technology applied to the dashboard.it utilizes the advantages of high energy density, non-contact processing and small thermal influence of the laser, and is used for processing micropores having a large aspect ratio to form a weakening line which does not affect the appearance.laser weakening equipment eliminates the visible wiring that matches the airbag cover and the dashboard, improving aesthetics and comfort.
vibration friction welding is a method of welding a frictional hot melt resin by a left and right vibration of a fixture under the condition that a pressure is applied to the upper and lower workpieces, and the welding method is combined with the workpiece under pressure curing. taking advantages of its good welding effect on large workpieces with irregular shape and complex shape, vibration friction welding is widely used in the welding of dashboard assembly.
with the development of automobile electronics technology, in addition to the initial functional lighting, automobile lighting has become more and more focused on comfort and personalized lighting.for example, the interior atmosphere lamp, which is a decorative lighting fixture, it can change its brightness and color according to the state of the vehicle, environment and personal preference, improving the passenger experience, and the car brand recognition.when driving at night, the interior atmosphere lights can reduce visual fatigue and improve the driving safety to a certain extent.
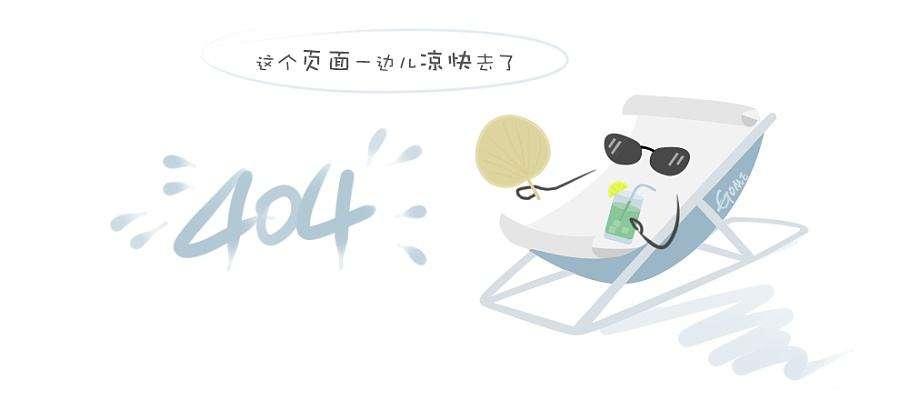